Technology

BioRMB™ - Biologic Real Moving Bed
Overview
Biologic Real Moving Bed (BioRMB™) is a patented ChromaTan technology which utilizes a column free system of continuously moving resin slurry which simultaneously performs the steps of your chromatographic method. This results in a steady state continuous purification of product, intensifying your chromatographic process. By mobilizing the stationary phase and operating counter currently your product yield and purity can be optimized in ways not possible in packed bed chromatography.
The technology relies on a flow path comprised of large pore hollow fiber membranes which retain the resin but allow load material and buffers to counter currently pass through the moving slurry. This allows the molecule of interest to bind in low pressure static conditions and buffers to pass through the slurry in a high volumetric ratio resulting in increased yields and improved contaminant removal.
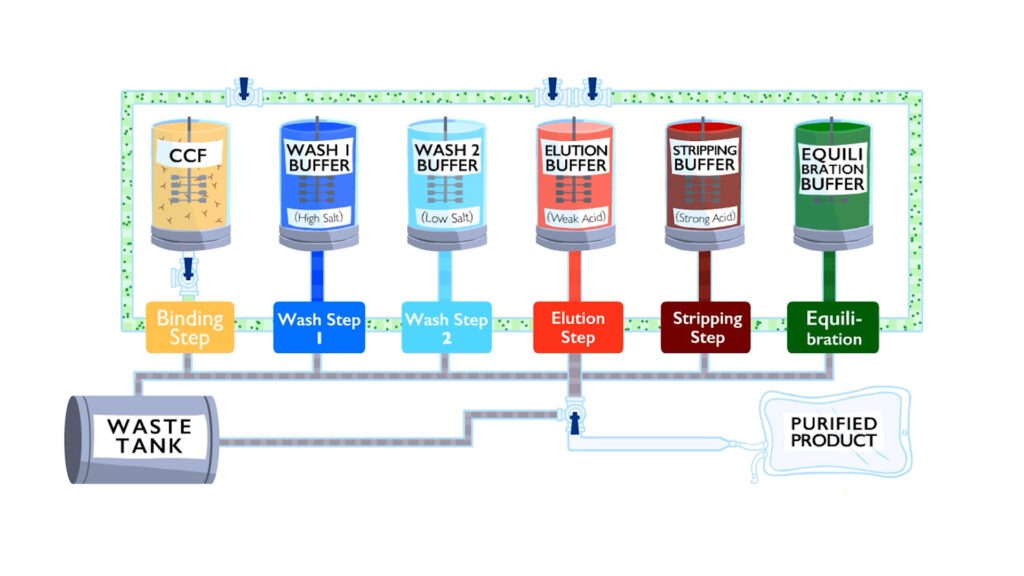
Featuring true steady-state, low-pressure operation, a 10X decrease in resin use, and a fully closed, disposable flowpath
BioRMB™ gives the user more dynamic control and increased degrees of operating freedom versus traditional packed bed chromatography. By mobilizing the typically stationary resin phase as a slurry and precisely controlling the buffer to resin flow rate ratio (γ or Gamma) the system can address the most challenging purifications.
The system is resin agnostic, allowing the use of any low density bead larger than 12 micron, opening up the window to smaller bead sizes than are traditionally used in analytical chromatography applicatoins. There is no limitation to aqueous chemistries for biologic applications encompassing affinity, ion exchange, hydrophobic interaction and mixed mode chemistries. Additionally, the technology is equally adept at initial product capture or in polish applications running in Bind/Elute or Flow Through operations.
The conveyor belt-like operation requires a very low volume of resin which is cycled continuously, creating a hyper efficient mode of purification. This results in a 10 to 15 fold increase in productivity as measured by product amount purified per liter of resin per hour (grams of product /L resin/hour). The higher productivity lowers cost of goods, particularly in early phase clinical production where packed bed columns are often sized for throughput, and only run a limit number of cycles, never reaching their maximum lifetime.
BioRMB™ technology lends itself to process intensification, allowing for inline concentration of your cell culture feed or continuous IVT reaction. Additionally, operating at steady state enables online buffer neutralization and continuous process analytics.
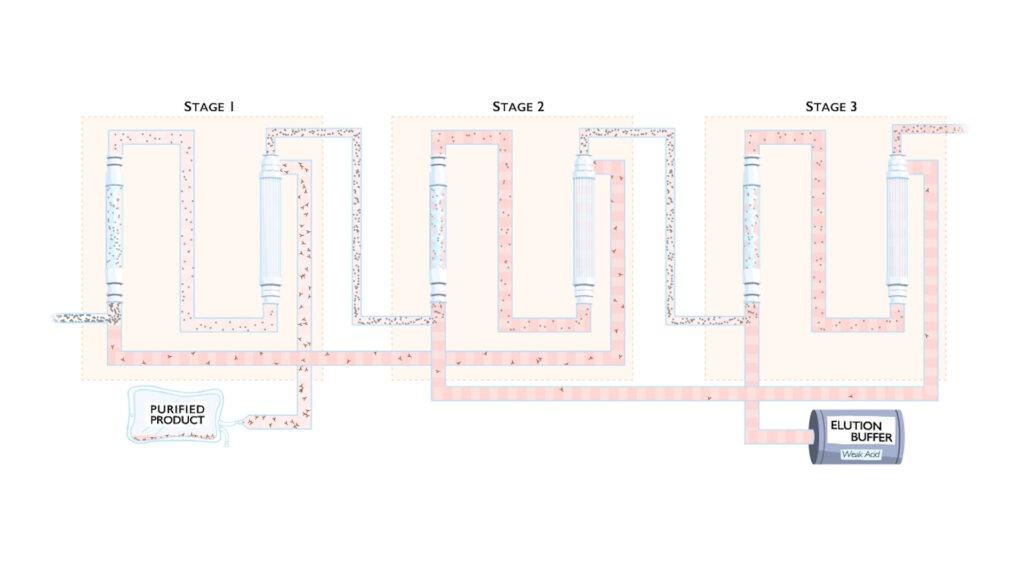
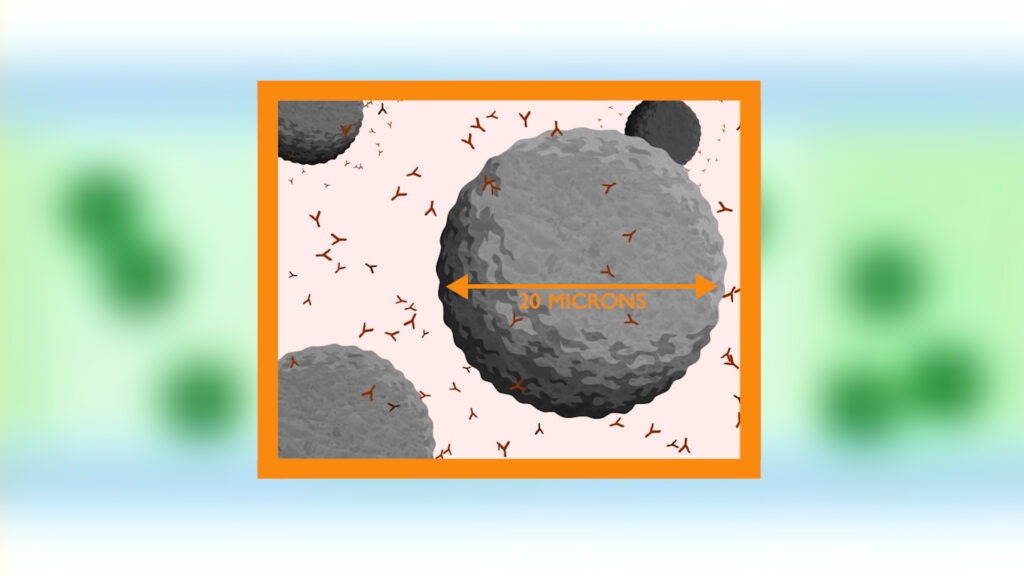
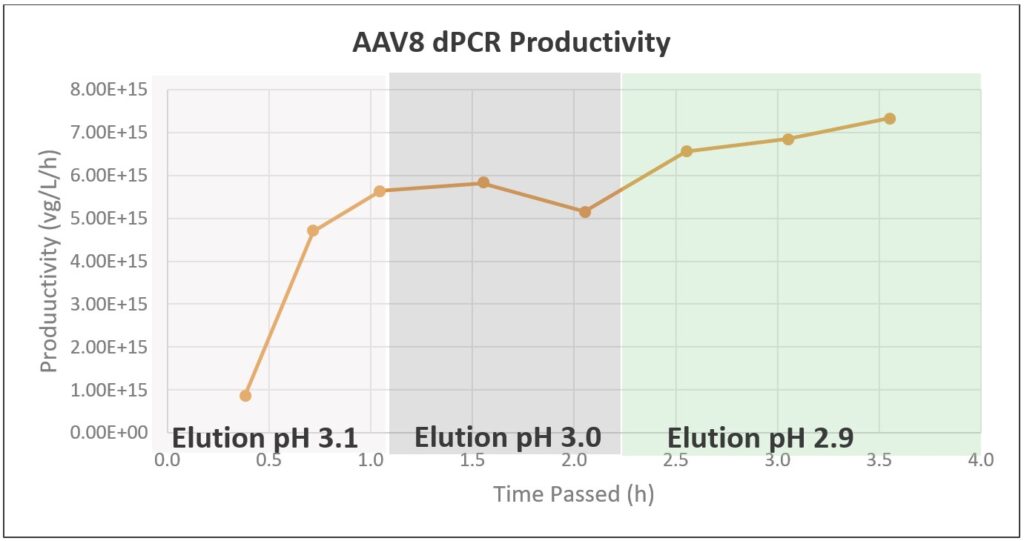
BioRMB™ Software Control
All BioRMB™ systems ship with a comprehensive application suite which streamlines the entire chromatography process, from recipe design all the way through data analysis. Our guided recipe design software suggest configurations to hit your washout targets while minimizing buffer consumption, and seamlessly feeds into the chemical process modelling utility which you can use to design buffer recipes optimized for the BioRMB™ platform. Recipes can be loaded in the system control software directly from the recipe editor, allowing an operator to step through the process sequence without opportunities to deviate from your process development team’s run plans. Online sensor data is collected in a SQL database where it can be visualized wih high performance, interactive dashboards during and after your runs.
All of these components are provided as web services available on your equipment, without any additional servers or workstations to administer. Simply connect your new BioRMB™ machine to your network and connect to the system with any modern web browser. For customers who prefer a native application, we provide a custom desktop client for easy, straightforward access to all of your equipment’s functionality.